一、裝置簡介
(一)裝置發(fā)展及其類型
?。保b置發(fā)展
聚苯乙烯樹脂(PS)是世界五大通用塑料之一,是熱塑性樹脂的主要品種,其產量僅次于聚烯烴和聚氯乙烯,在合成樹脂中占有重要地位。
聚苯乙烯樹脂的生產一般采用本體聚合、溶液聚合、乳化聚合、懸浮聚合等四種工藝。中國現有的懸浮聚合工藝技術,由于規(guī)模小、產品種類單一、原料單耗和能耗都較高,因而缺乏競爭力。致使在國際上,由于懸浮聚合工藝排放廢水量比較大,能耗、物耗高,也正在逐漸被本體聚合工藝所取代。
連續(xù)本體法已逐漸發(fā)展成為生產聚苯乙烯樹脂的一種常用方法,因為該方法能以較低的成本生產出純度高、殘留單體含量低的產品。流程中可以有1-5個反應器,其構型有多種。通常把苯乙烯、溶劑(乙苯),有時也有引發(fā)劑一起加入到第一個反應器中,反應器通常是在連續(xù)升溫下操作,操作溫度為90—180℃,最終轉化率可達60%—90%。反應流出物送人真空脫揮器,將殘留單體和溶劑蒸發(fā)掉,熔融聚合物擠出造粒,冷凝下來的未反應單體和溶劑經循環(huán)系統(tǒng)返回到反應器進料中。
我國從20世紀60年代開始生產PS,80年代開始從國外引進的技術和設備,使我國H工業(yè)得到不斷的發(fā)展和壯大。到2000年,我國PS生產能力已經達100X104t/a左右。
2.裝置的主要類型
連續(xù)本體聚合工藝的典型生產技術有德國BASF公司、美國Huntsman公司的臥式、立式釜工藝技術,美國DOW化學公司的高立式釜工藝技術,美國Cosden公司(現美國FINA公司)的臥式釜工藝技術,日本東洋工程公司一三井東亞公司(TEC—MTC)的矮立式釜工藝技術等工藝技術。
(二)裝置單元組成與工藝流程
1。組成單元
整個生產裝置由下列主要單元組成:
原料接受、儲存及配制系統(tǒng);切膠、溶膠及供料系統(tǒng);聚合系統(tǒng);脫揮發(fā)系統(tǒng);冷凝及抽真空系統(tǒng);造粒系統(tǒng);粒料輸送,儲存及包裝系統(tǒng);導生系統(tǒng);公用工程系統(tǒng)。
各單元介紹如下:
(1)原料接收、儲存及配制
苯乙烯單體從界區(qū)外批量送人本裝置苯乙烯罐中。當生產通用級GPPS產品時,苯乙烯經進料泵直接送到主進料泵的人口。當生產高抗沖級HIPS產品時,苯乙烯經進料泵送到漿液罐配制橡膠溶液并送至溶膠罐進行溶解,然后再送到主進料泵。
礦物油從界區(qū)外送來存人本裝置礦物油罐中,礦物油經泵送到主進料泵的人口管道,其流量由調節(jié)閥控制。
乙苯由界區(qū)外送至本裝置乙苯貯槽中。乙苯按需要補充到循環(huán)液中,循環(huán)液連續(xù)加入反應原料中。兩者共用循環(huán)液進料泵輸送。循環(huán)液送至主進料泵的入口。隨反應的進行,循環(huán)液不斷循環(huán)使用,其中的雜質不斷增多,需定期將部分循環(huán)液送回苯乙烯裝置回收處理。當反應系統(tǒng)中需注入循環(huán)液或乙苯時,可通過泵經過過濾器向反應系統(tǒng)供料。
聚合反應使用的引發(fā)劑是TBPB或DP—275B,它是用乙苯和礦物油配成的溶液,可以直接使用。將桶裝引發(fā)劑用泵送到引發(fā)劑供料槽中。經引發(fā)劑供料泵計量送到第一反應器。聚苯乙烯需加入抗氧劑及硬脂酸鋅等粉狀固體添加劑。按比例將它們加到添加劑槽中,槽中預先加入定量的循環(huán)液,攪拌器及循環(huán)泵使添加劑均勻的懸浮于循環(huán)液中,懸浮液用添加劑供料泵計量送到第二反應器中部。
(2)切膠、溶膠及進料準備
①切膠、溶膠
橡膠是以25—34kg一塊裝成木箱運來的,直到使用時才從箱中取出膠塊。聚丁二烯橡膠冷流會導致膠塊變形。可能變成不適于進入到切膠系統(tǒng)的形狀。
苯乙烯用泵連續(xù)送到漿液罐的底部,使苯乙烯與橡膠形成漿液。只要切膠在進行,苯乙烯就一直連續(xù)輸送。對不同牌號的產品切膠量以及與其相關的苯乙烯的量是不同的。苯乙烯—膠混合物由漿液泵送到溶膠罐。
從溶膠罐出來的膠液直接流到主進料泵,在那里它按要求和其他物質混合,形成反應器的主要供料。
?、诠┝蠝蕚?/p>
從主進料泵出來的物料過濾后經計量提供聚合反應的主供物料流。主供料預熱到80℃左右,進入第一反應器。生產抗沖級產品時,預熱后的一部分物料經進料泵送到第二反應器的中部,此股物料稱為M2進料。
(3)聚合系統(tǒng)
本單元由幾個串聯的反應器組成,物料連續(xù)的從低溫區(qū)流向高溫區(qū),溫度范圍在90-180℃之間。反應所產生的聚合熱是經換熱載體實現熱交換的。反應器一般都設有攪拌,實現共混及反應均勻。最終產品轉化率可達80%—85%。
(4)脫揮發(fā)系統(tǒng)
從最終反應器擠出的物流中約含有80%—85%的聚合物,15%—20%的液體,這股物料經減壓后,到聚合物加熱器中,在很短的時間內聚合物溫度從180qC加熱到230℃,然后落到一個帶夾套的脫揮發(fā)物器中,該脫揮發(fā)物器操作處于負壓狀態(tài),絕壓一般控制在30mmHg以下,以除去聚合物中的溶劑乙苯和未反應的苯乙烯。脫揮發(fā)物器底部的聚合物泵把熔融狀態(tài)的聚合物送到擠壓模頭進行造粒。
(5)冷凝及真空系統(tǒng)
從脫揮發(fā)物器脫除的苯乙烯、乙苯等物料蒸汽先進人部分冷凝器,物料中少量的焦油即苯乙烯的齊聚物等在此冷凝下來,流人焦油收集罐。物流中未冷凝下來的蒸汽進入最終的冷凝器,使苯乙烯、乙苯冷凝下來,所形成的冷凝液就是工藝物料的循環(huán)液,可循環(huán)使用。
(6)切粒系統(tǒng)
由聚合物齒輪泵送出的熔融聚合物經模頭擠出,條料分別進入水浴槽進行冷卻。經固化后的條料從水浴槽中拉出,經干燥后進人切粒機。模頭處設排風罩以抽出從模頭擠料時揮發(fā)出來的小分子。
(7)粒料輸送、儲存及包裝系統(tǒng)
從切粒機出來的粒料經振動篩分出過大或過小的粒子或團料后,合格的進入料斗,經旋轉閥送到輸送料管,輸送風機將帶有粒料的氣流輸送至料倉。一般GPPS和HIPS產品料倉應分別儲存相應的粒料,不能混用。普通級產品和抗沖級產品分別由兩條推拉系統(tǒng)從料倉送至包裝作為成品。
(8)熱載體系統(tǒng)
整個工藝過程中,原料的預熱器,反應器的盤管和夾套,脫揮發(fā)物器夾套及聚合物加熱器,聚合物輸送管道,部分冷凝器等都需要熱載體與其中的物料進行熱交換。熱載體的使用溫度一般有三種,一種是冷載體,溫度在60℃左右,一種是熱載體,溫度在2000℃左右,第三種是過熱載體,溫度在280℃左右。整個反應的原料預熱、聚合、真空系統(tǒng)的部分冷凝等需要前兩種溫度的載體經混合后,由調節(jié)閥控制所需的換熱。過熱載體主要是加熱聚合物加熱器和脫揮發(fā)物器,以及部分物料管線。熱載體的熱量由兩臺加熱爐提供。整個熱載體系統(tǒng)的不同溫度是靠換熱器來實現溫度控制的。
(9)公用工程系統(tǒng)
裝置公用工程主要包括:高、低壓氮氣、儀表風及雜用風、蒸汽、循環(huán)冷卻水、激冷水、消防水等。主要用于裝置吹掃、壓料;調節(jié)氣動閥門和切粒設備;加熱物料;冷卻換熱器;滅火、罐區(qū)降溫等。
2.工藝流程
聚苯乙烯生產工藝原則流程見圖5—3。
苯乙烯和其他的供料成分經預熱后連續(xù)供到串聯的反應器中,在這里大部分苯乙烯單體被轉化成聚合物。根據產品牌號的不同進料組成有所不同。進料中一般含有:苯乙烯和乙苯,其中乙苯是一種鏈轉移劑,還有各種產品添加劑,聚合反應的化學引發(fā)劑,在生產高抗沖級產品時,進料還必須含有聚丁二烯橡膠。
物料在進入反應器之前,要在預熱器中進行預熱。在第一反應器還要進一步供熱以引發(fā)聚合反應。其他的反應區(qū)要冷卻,以除去聚合熱和控制反應速率。進料和反應器中的物:料是通過控制在一定溫度下的熱載體的循環(huán)進行加熱和冷卻的。從反應器中出來的產品在脫揮發(fā)物器中進行加熱和抽真空以便除去乙苯和沒有反應的苯乙烯。從最終反應器出來的聚合物在聚合物加熱器中進一步加熱,這樣有助于脫除揮發(fā)分和把聚合物保持在適于泵送的黏度下。
揮發(fā)出來的物質在真空系統(tǒng)(一級或兩級)的抽真空下經過冷凝系統(tǒng)回收。部分冷凝器把進入最終冷凝器之前的蒸汽冷卻,并且除去了其中少部分蒸汽壓很低的象苯乙烯的齊聚物之類的組分。最終冷凝器回收了基本是所有剩余的苯乙烯和乙苯,這部分冷凝液在作為循環(huán)液進入聚合反應系統(tǒng)之前,先返回到儲罐中儲存。
脫除揮發(fā)分的聚合物熔體,由齒輪泵送到擠出模頭,擠出的聚合物條料經水浴槽拉人切粒機,切出的產品顆粒經過篩子和磁鐵,除去過大的顆粒和金屬碎屑。
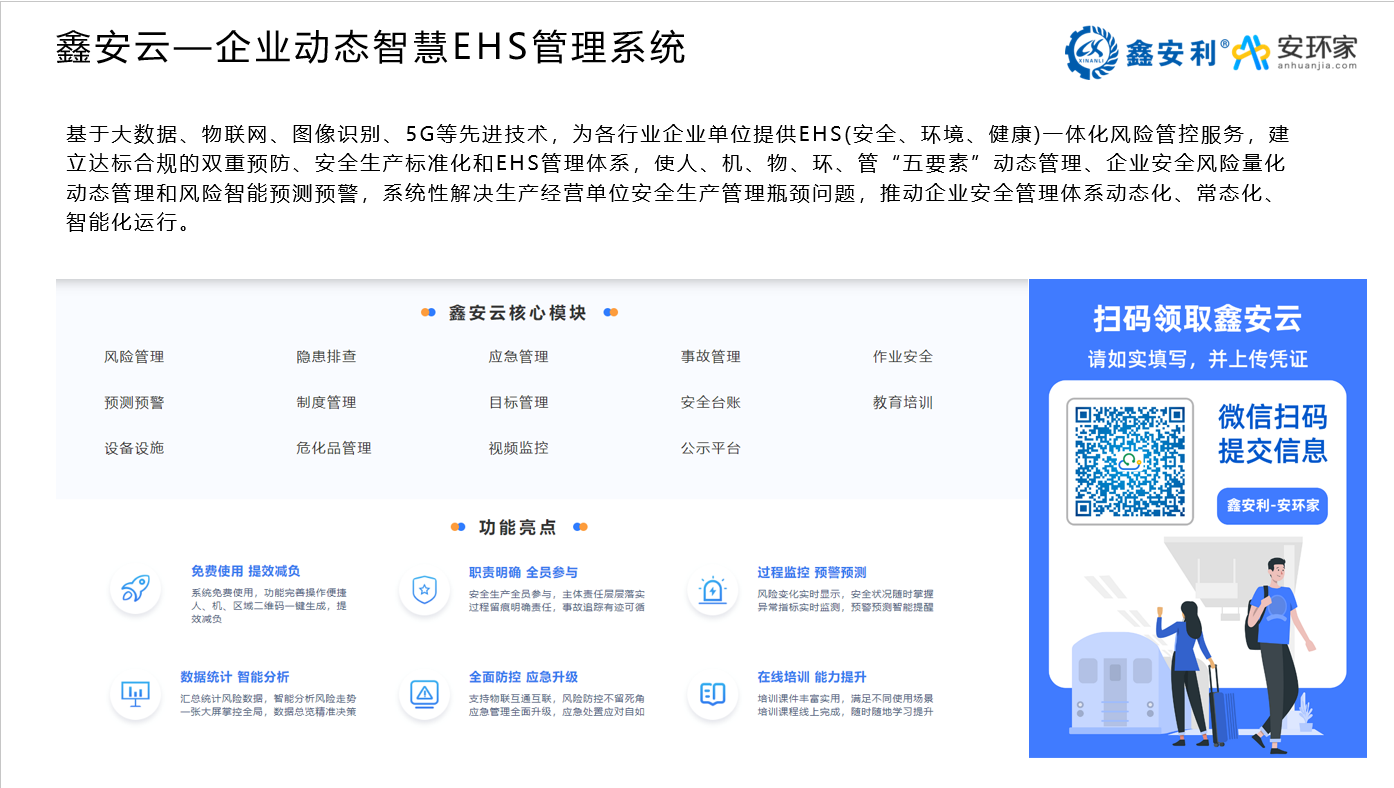